Introduction
The Itasca Constitutive Model for Advanced Strain Softening (IMASS) has been developed to represent the rock mass response to excavation induced stress changes. IMASS represents the damage around slopes, caving processes, pillars, open stopes, and other excavations; it does this by accounting for the progressive failure and disintegration of the rock mass from intact, jointed, and/or veined rock to a disaggregated, bulked material. IMASS is based on empirical relationships and uses strain and zone-size dependent properties that reflect the impacts of dilation and bulking as a rock mass undergoes plastic deformation. Based on the CaveHoek constitutive model, developed by Itasca consultants in 2010 (Pierce, 2013), IMASS is the product of many successful engineering consulting projects and brittle rock behavior research. IMASS is the default constitutive model for mining applications at Itasca due to its powerful features and ability to closely mimic the behavior of rock mass under complex stress paths.
IMASS uniquely contains two softening (or residual) yield envelopes to represent the two-stage softening behavior for a rock mass that distinguishes between damage (caused by fracturing and the associated loss of cohesion and tensile strength) and the subsequent disturbance (due to bulking) in rock mass behavior. This two-stage softening/weakening behavior in IMASS is critical to accurately represent the rock mass post-peak behavior for underground and surface mining applications.
IMASS uses the latest Itasca constitutive model framework and techniques for apex correction, automatic testing, and property update and management. IMASS is available as a built-in, optional constitutive model for use in both FLAC3D and 3DEC (version 7.0 or later) and is sold as a separate, monthly or annual lease, license.
Rock Mass Response to ExcavationIMASS captures the overall process of loading the rock mass to its peak strength, followed by a post-peak reduction in strength to some residual level with increasing strain. This often is termed a “strain-softening” process and is the result of strain-dependent material properties.
Figure 1 shows a conceptual model of the rock mass response to caving where an overall strain-softening model can represent such material behavior and how it correlates to the different states of the rock mass response.
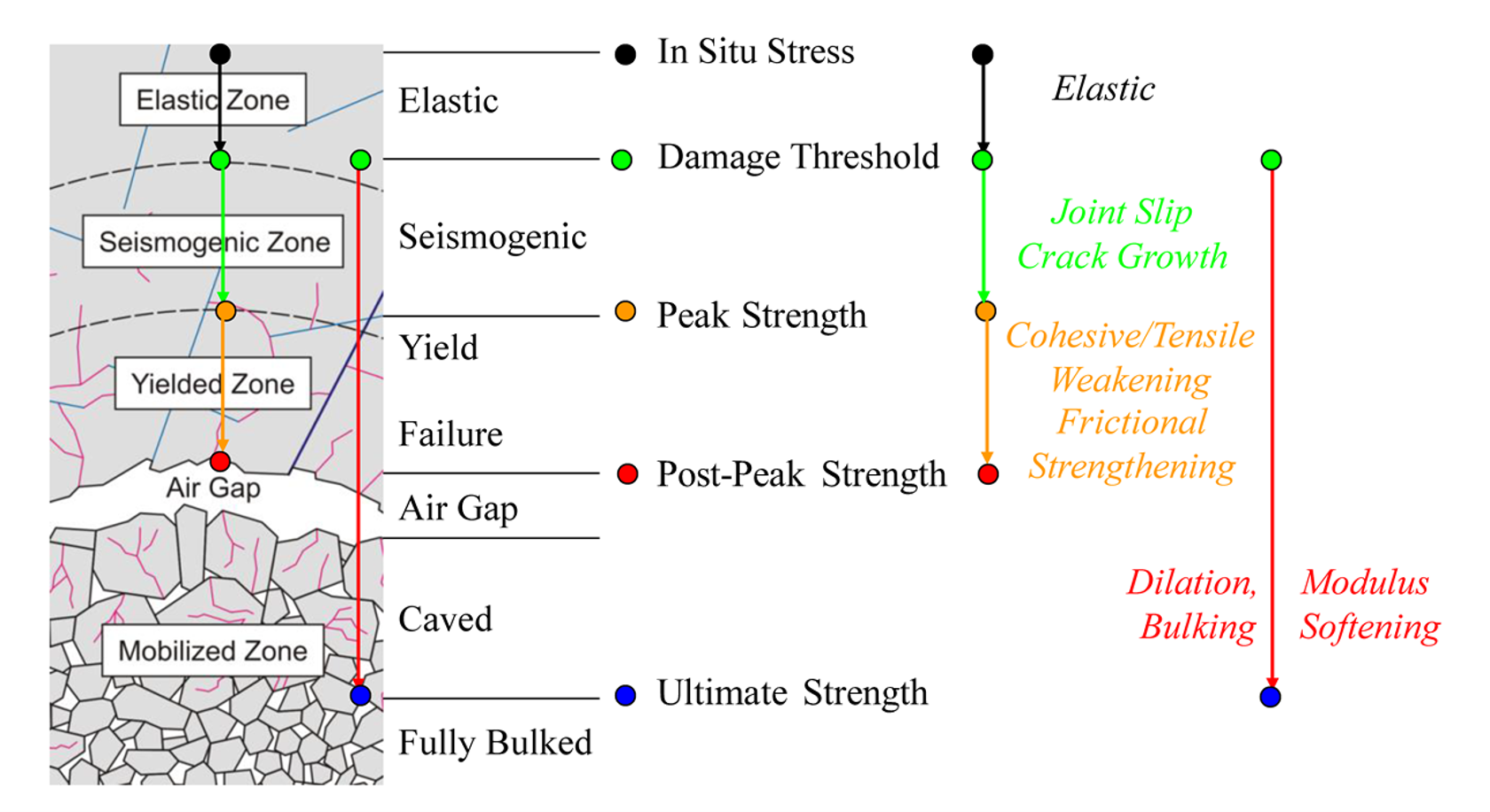
The four most critical factors from Figure 1 that control the overall behavior of the rock mass during excavation are summarized below.
Cohesion and Tension Weakening and Frictional Strengthening: As the rock mass deforms it undergoes a reduction in strength from its peak in-situ value to a lower residual value. In general, massive to moderately jointed rock masses weaken by fracturing and the associated loss of cohesion and tensile strength but also have the ability to strengthen when even lightly confined due to a combination of friction mobilization and dilation resulting from bulking – the spatial rearrangement of blocks and increasing porosity – of the fractured rock. These mechanisms largely occur in sequence (Kaiser et al. 2015)1.
Post-Peak Brittleness: The rate at which the strength drops from peak to residual as the loaded material accumulates plastic deformation is referred to as brittleness. Rocks that maintain their peak strength with continued loading are referred to as perfectly plastic (ductile). Rock masses that instantaneously drop to residual strength properties when they exceed their peak strength are referred to as perfectly brittle. In consequence, the brittleness controls how fast or slow the stresses are shed away from the yielded rock mass with accumulated strain.
Modulus Softening: The rock mass increases in volume as intact rock blocks fracture, separate, and rotate during the yielding and mobilization process. As the rock mass bulks, a reduction in modulus is expected to occur. Representing this decrease in stiffness is crucial for assessing the evolving stress state around the cave and underground openings since, as rock mass dilates/bulks, its ability to carry stress (for a given amount of elastic deformation) decreases.
Dilational Behavior: Dilation is the change in volume of a rock that occurs with shear distortion. An accurate assessment and representation of the dilational behavior of a jointed rock mass is essential to predict the correct volume increase during plastic deformation. This will impact the confinement-dependent strength of the rock mass.
IMASS Background
IMASS incorporates a Hoek-Brown peak rock mass strength envelope and two softening (residual) yield envelopes as shown in Figure 2:
- The peak strength envelope (solid, red curve) is defined by the generalised Hoek-Brown criterion (Hoek et al. 2002).
- The first and second residual envelopes describe the behavior of cohesionless, perfectly frictional material with different degrees of interlocking.
- The first residual envelope represents the post-peak rock mass strength (dashed, blue curve). At this point, the rock mass is assumed to have undergone fracturing but the resulting rock fragments are still fully interlocked and porosity is still considered to be zero.
- The second residual envelope represents the rock mass ultimate residual strength (dotted, green curve). At this point the degree of rock fragment interlocking is at its minimum and the porosity is considered to be at its maximum (of up to 40%).
The rock mass response in terms of stress-strain behavior in IMASS is shown in Figure 3, which summarizes the scale that is used for softening/weakening of the rock mass between peak to post-peak and then between post-peak and ultimate strength envelopes.
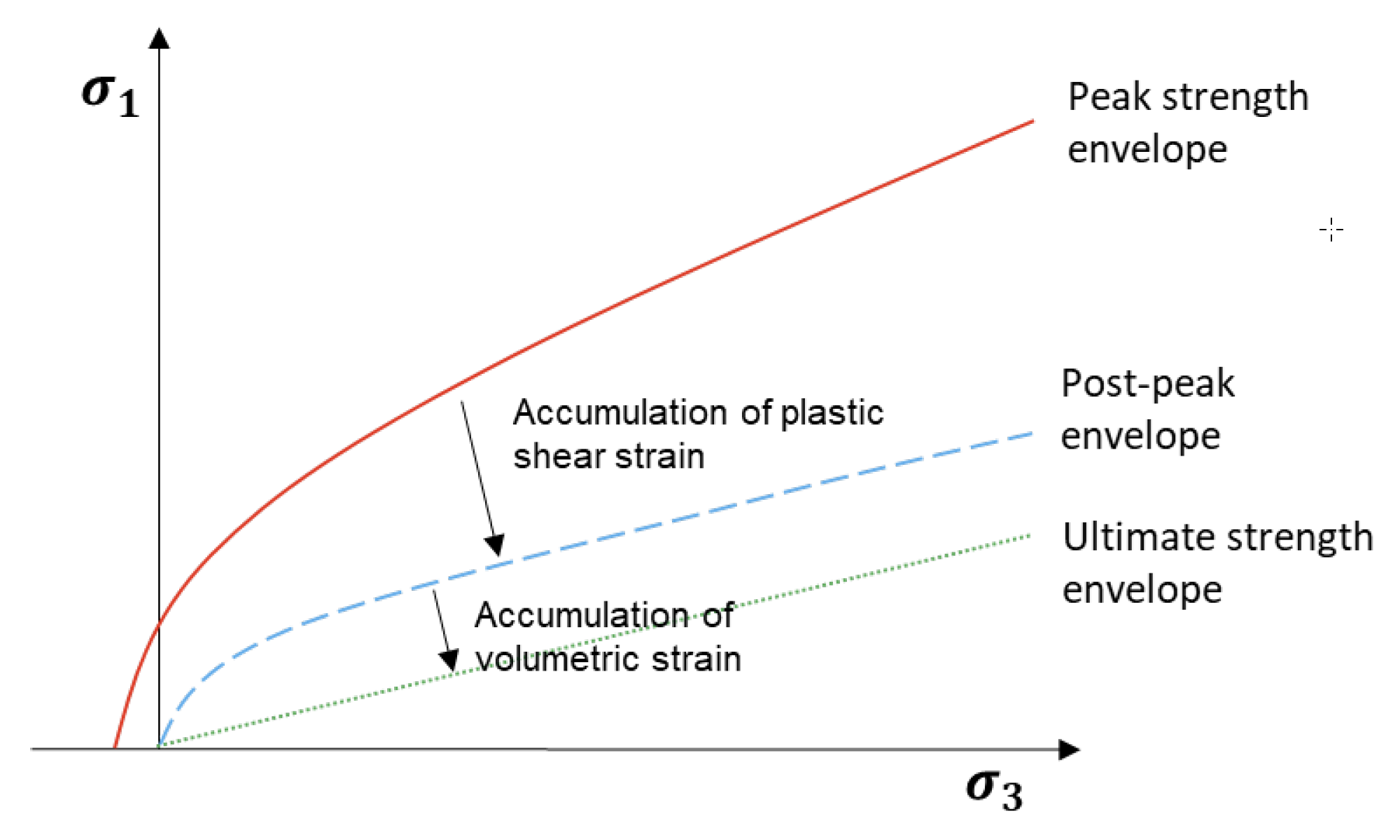
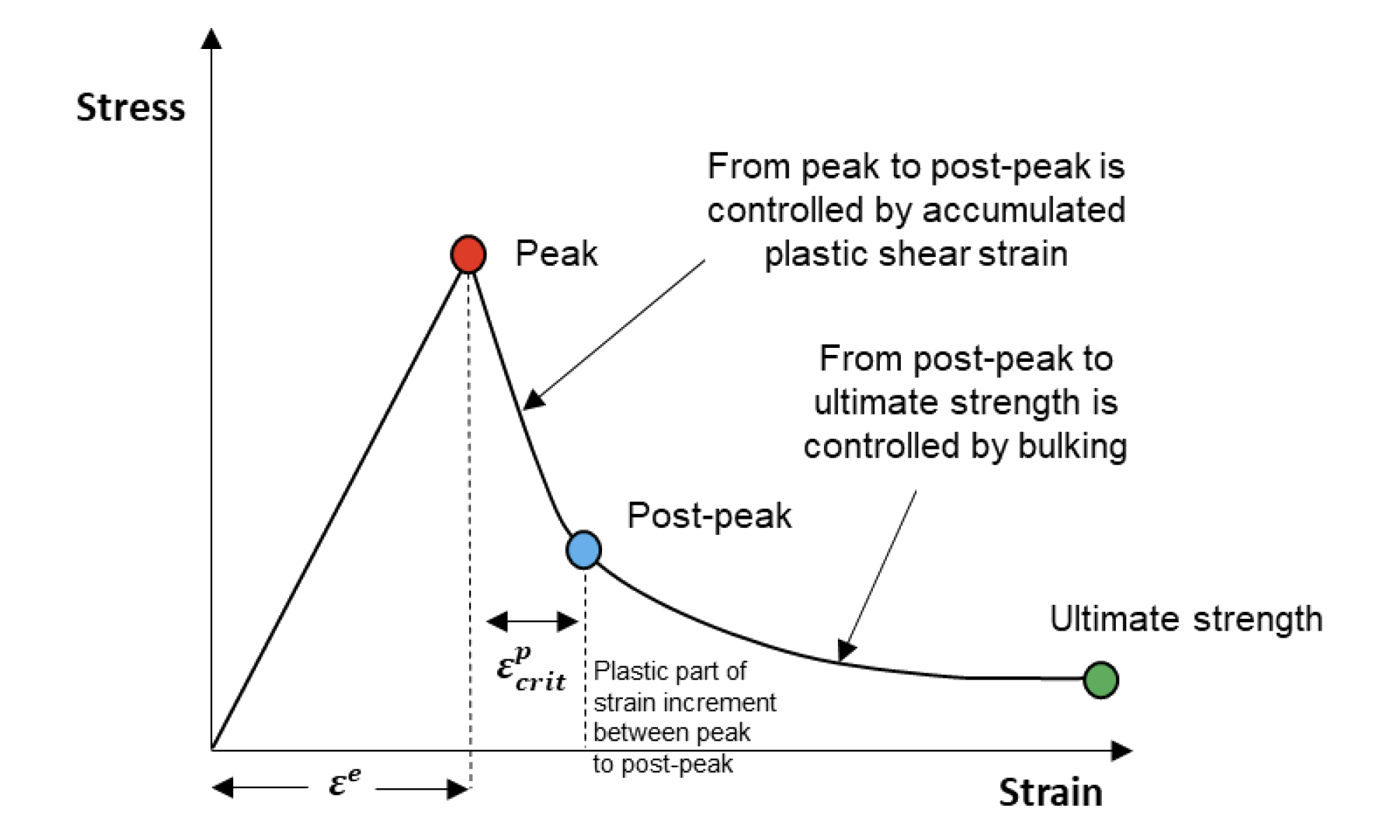
During Phase 1 (peak to post-peak):
- Damage is the result of fracturing of intact rock due to stress changes. This causes only negligible increases in porosity and permeability.
- Loss of strength results from small strain processes.
- The numerical assessment of damage is dependent on the accumulation of plastic shear strain. Phase 1 ends once the rock mass has reached the “critical plastic shear strain” and its strength equals the post-peak strength.
During Phase 2 (post-peak and ultimate strength):
- Additional straining and disturbance are the result of rearrangement of rock blocks and cause a significant increase in porosity (up to 40%) and permeability.
- Loss of strength results from large-strain processes.
- The numerical assessment of disturbance is dependent on the accumulation of volumetric strain. Phase 2 ends once the rock mass has reached the “maximum volumetric strain”. At this point,the rock mass has reached its ultimate residual strength and its strength won’t evolve further with additional straining.
IMASS uses strain and zone-size dependent properties that are adjusted to reflect the impacts of dilation and bulking as a rock mass undergoes plastic deformation incorporating:
- rock mass yielding
- modulus softening
- density adjustment
- dilation, inclung dilation shut-off
- scaling of properties to zone-size
- cohesion weakening
- tension weakening
- frictional strengthening
Weakness planes can also be defined by using the Ubiquitous Joint approach (Clark 2006) within IMASS. This formulation accounts for the presence of closely spaced planes of weakness (e.g., veining). The criterion for failure on these planes, whose orientation is given, consists of a composite Mohr-Coulomb envelope with tension cut-off. Tensile strength, cohesion and friction angle control the shape of the Mohr-Coulomb envelope, while dip and dip direction are set to represent true dip and dip direction of the structure or joints.
For More InformationFor details about the IMASS constitutive model, refer to our online software documentation, read the technical paper in the MassMin2020 proceedings by Ghazvinian et. al, 20202 , or watch the following presentation by Dr. Ehsan Ghazvinian.
As an empirical model, IMASS includes a wide number of parameter default values, based on Itasca's experience, making it easy to start using. For example, after specifying IMASS as the constitutive model using the following commands:
FLAC3D | 3DEC |
model config imass zone cmodel imass |
model config imass block zone cmodel imass |
Only the following six parameters need to be defined via the FLAC3D or 3DEC commands shown below:
- Density
- Geological Strength Index | GSI
- Intact uniaxial compressive strength | UCSi
- Hoek–Brown material constant (intact rock) | mi
- Intact rock modulus | Ei
- Multiplier for critical plastic shear strain
FLAC3D | 3DEC |
zone initialize density [_density] zone property in_stren_gsi [_gsi] zone property in_stren_ucsi [_ucsi] zone property in_stren_mi [_mi] zone property in_mod_youngintact [_Ei] zone property in_weak_multecrit [_ecrit] |
block zone property density [_density] block zone property in_stren_gsi [_gsi] block zone property in_stren_ucsi [_ucsi] block zone property in_stren_mi [_mi] block zone property in_mod_youngintact [_Ei] block zone property in_weak_multecrit [_ecrit] |
However, all the flags or input parameters in the constitutive model (Table 1) are accessible to permit for model calibration. Because IMASS is being actively used and enhanced through experience and research at Itasca, it has a versioning system. The current version may be read as a model parameter.
Table 1: IMASS material property names
Flags/Inputs | Calculated | Emergent | |
---|---|---|---|
Peak | flag_stren_mod(off) | calc_stren_global | |
strength | in_stren_gsi | calc_stren_tension | |
in_stren_mi | calc_stren_ucsrm | ||
in_stren_ucsi | calc_stren_mb | ||
calc_stren_s | |||
calc_stren_a | |||
Modulus | in_mod_youngintact | calc_mod_youngrm | emer_mod_young |
calc_mod_poisson | |||
Strength Weakening | flag_weak_barton(on) | calc_weak_ecrit | emer_weak_sloss |
flag_weak_tencut(on) | calc_weak_zsize | emer_weak_esplastic | |
in_weak_multecrit | emer_weak_istenweak | ||
in_weak_chmbr(4.33) | emer_stren_mcfric | ||
in_weak_char(1.0) | emer_stren _mccoh | ||
in_weak_phib(30) | emer_stren _mcten | ||
in_weak_sloss(1.0) | |||
in_weak_tabletension | |||
Dilation/Bulking and Modulus Softening | flag_bulking_denadj | emer_bulking_mcdil | |
flag_bulking_modsoft | emer_bulking_den | ||
in_bulking_den | emer_bulking_totvsi | ||
in_bulking_dil | |||
in_bulking_targetvsi | |||
in_bulking_maxtotvsi(2/3) | |||
Stress at Failure | flag_sfail_failtrack(off) | emer_sfail_pmax | |
emer_sfail_plungepmax | |||
emer_sfail_trendpmax | |||
emer_sfail_pmid | |||
emer_sfail_plungepmid | |||
emer_sfail_trendpmid | |||
emer_sfail_pmin | |||
emer_sfail_plungepmin | |||
emer_sfail_trendpmin | |||
Ubiquitous Joint | flag_uj_usejoints(on) | emer_uj_esplastic | |
in_uj_jcoh | |||
in_uj_jdil | |||
in_uj_jfric | |||
in_uj_jten | |||
in_uj_jdip | |||
in_uj_jddirection(on) | |||
in_uj_jnx | |||
in_uj_jny | |||
in_uj_jnz | |||
1Kaiser, P., R. Bewick, F. Amman, and M. Pierce (2015). "Best Practice in Rock Mass Characterization for Brittle Rock Masses," Rio Tinto Centre for Underground Mine Construction, copyright Rio Tinto.
2Ghazvinian, E., T. Garza-Cruz, L. Bouzeran, M. Fuenzalida, Z. Cheng, C. Cancino, and M. Pierce (2020). "Theory and Implementation of the Itasca Constitutive Model for Advanced Strain Softening (IMASS)," in Proceedings Eighth International Conference and Exhibition on Mass Mining (MassMin 2020): Santiago).